Understanding mining methods is fundamental to assessing potential investments in the mining sector. These methods are not simply technical procedures; they are vital to evaluating the viability, safety, and profitability of mining projects.
There are two broad categories of mining methods: surface mining and underground mining. Surface mining involves extracting minerals from the earth’s surface and is often chosen for mineral or ore deposits that are near the surface. This method is usually more cost-effective for suitable deposits but has a large environmental footprint. Underground mining, on the other hand, is required for accessing deeper mineral deposits and has a smaller surface footprint. It involves digging into the earth and is generally used for deposits that are too deep to be mined by surface methods.
In this article, we will look at both surface mining and underground mining, the different types of each, and the situations in which one might be selected over another.
What is a Mining Method?
A mining method is a specific process or technique used to extract ore from the ground in a safe and efficient manner. “Ore” in this context refers to rock that contains enough target mineral(s) that makes it economic to mine and process. The selection of a mining method is influenced by various factors, including the safety and efficiency it offers, the mine’s location and depth, the surrounding geology, economic considerations, and environmental impact.
The type of mineral or metal being excavated is critical to mining method selection. Certain minerals are more likely to be found in specific types of deposits that are more broadly suitable for either surface or underground mining, and specific methods within those categories. For example, open pit mining is more commonly associated with hard-rock commodities, such as gold and copper, commonly found in RCF portfolios. Other specific considerations include:
- Depth of the deposit: Surface mining is preferred for shallow deposits, while deeper deposits necessitate underground mining (provided the ore grade is high enough).
- Economic considerations: The cost-effectiveness of the extraction process versus potential revenue from the mined material is crucial.
- Environmental impact: Mining operations must comply with environmental regulations, and the environmental impact can influence the choice of mining method.
- Safety considerations: Including risk assessments around geotechnical stability, mining rate, workforce experience, gas leaks, etc.
- Orebody angle: known as the “dip,” the angle at which an orebody, rock layer, or geological stratum inclines from the horizontal can influence the direction of the mining process, drilling and blasting techniques, and the choice of method used.
- Geological conditions: The physical and chemical characteristics of the orebody and surrounding rock, including ground stability, play a significant role in determining the appropriate mining method.
Miners evaluate all these factors to decide the most efficient, safe, and economically viable method for extracting minerals. This careful consideration aims to ensure that mining activities are not only profitable but also sustainable and responsible.
The Role of the RCF Technical Team in Assessing Mining Assets and Methods Used
When assessing potential new investments, it is imperative for investors to understand the proposed mining methods being considered, and implications for the commercial success of the project. Metals and minerals are not monolithic. Different commodities require different mining methods based on a comprehensive set of variables. The RCF Technical Team is an in-house, multi-disciplinary team comprised of knowledgeable experts across, geology, metallurgy, engineering, ESG, and other key disciplines. They provide technical review across all phases of mining and will assess mining methods for cost, efficiency, safety, and other major factors. In those situations when a new project has not yet completed a pre-feasibility study, The RCF Technical has the experience to form its own view of what operating costs and capital costs will be based on different scenarios. This allows investment teams to evaluate data and form a proprietary view on the investment opportunity. In some cases, RCF adds value by identifying opportunities to change, adapt, or modify the mining method in ways that will improve the outcome for the mining company and limited partners.
Surface Mining Methods
Surface mining is used to extract minerals near the earth’s surface and involves removing the rock and soil known as the overburden from above a deposit to allow access to the ore. Surface mining methods account for more than two-thirds of the world’s yearly mineral production1 and approximately 90% of non-fuel mineral resources mined in the US2. Common metallic ores extracted through surface mining methods include bauxite for aluminum, hematite, and magnetite for iron, and chalcopyrite for copper3.
Compared to underground mining, surface mining is often preferred by mining companies as it is less expensive, safer, and entails fewer complications in terms of electricity and water. However, the larger footprint of surface mines often entails more land disturbance, so greater care needs to be taken to mitigate habitat destruction, erosion, and visual impact concerns. Also, surface mining is typically characterized by higher water consumption and in some cases is more polluting.
Advantages of Surface Mining
- Cost efficiency4: Surface mining is generally more cost-effective than underground mining. The extraction process is less complex and requires less capital and operational investment.
- Safety5: Generally, surface mining is considered safer for miners compared to underground mining, which has risks associated with unstable ground conditions and air quality.
- Higher production rates: Surface mining can extract larger volumes of minerals over a shorter period due to easier accessibility and larger-scale operations.
- Simpler logistics and ventilation requirements: There is no need for complex underground systems for ventilation, lighting, and ore haulage.
Disadvantages of Surface Mining
- Environmental impact6: Surface mining has a more significant environmental footprint, causing habitat destruction, landscape alteration, and potential water pollution.
- Limited depth of extraction: Surface mining can only access minerals located relatively near the earth’s surface.
- Visual and noise pollution: Large open pits, waste heaps, and heavy machinery can lead to scenic impact and increased noise levels which may or may not be an issue depending on the location of the operation relative to local communities.
Surface Mining Methods
Surface mining can be broadly divided into mechanical and aqueous methods. Mechanical mining methods are characterized by the use of large machines like excavators, bulldozers, drills, and shovels to remove overburden and extract ore. Aqueous methods, on the other hand, use water as a key component in the process of extracting minerals from the earth.
Open-pit Mining7
Open-pit mining is a method used to extract ore near the surface of the earth that results in a wide, open pit. This is the most common mining method that RCF sees as we evaluate potential assets, because it is used extensively across all hard-rock commodities including iron ore and gold, as well as many of the commodities critical to energy transition such as copper (also a hard-rock ore), nickel, zinc, and lithium.
Production drilling is completed using top-hammer or down-the-hole drills, followed by blasting. Waste and ore are mined using an excavator, face shovel, or loader. Excavation is made in “benches,” the step-like excavations formed as a result of the removal of rock or minerals, then in “cutbacks,” new levels or layers, which involves excavating and removing additional material from the pit’s walls or sides, and waste hauled out of the pit.
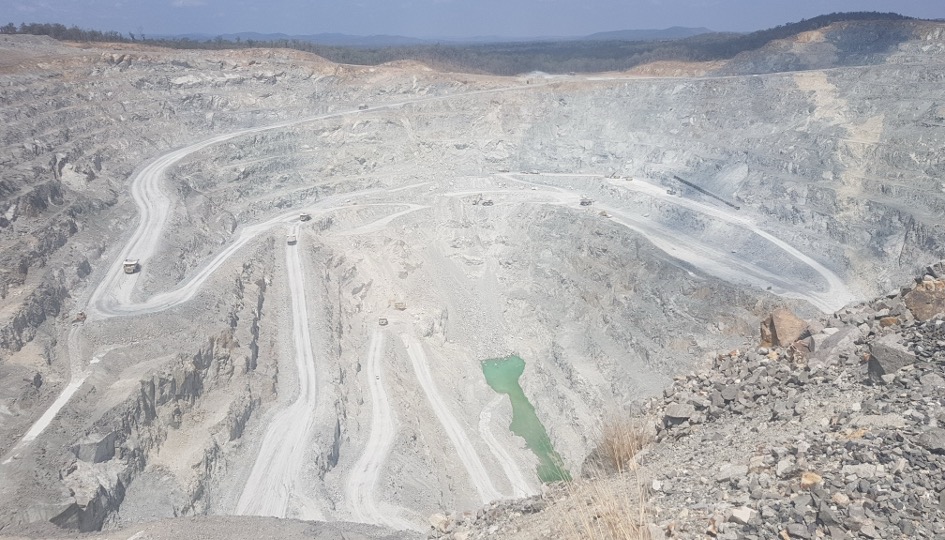
Dredging8
Dredging is the process of removing sand, gravel, or other sediment from the bottom of bodies of water. It uses a floating platform equipped with a suction hose or mechanical digging apparatus to extract sediment from the water body and then process it to extract the desired minerals. This technique is especially useful in placer mining, where valuable minerals are found in loose sediment in water bodies. The environmental impacts of dredging can be significant, including disruption of aquatic ecosystems and water turbidity. Therefore, careful management and environmental controls are often required to minimize these impacts.
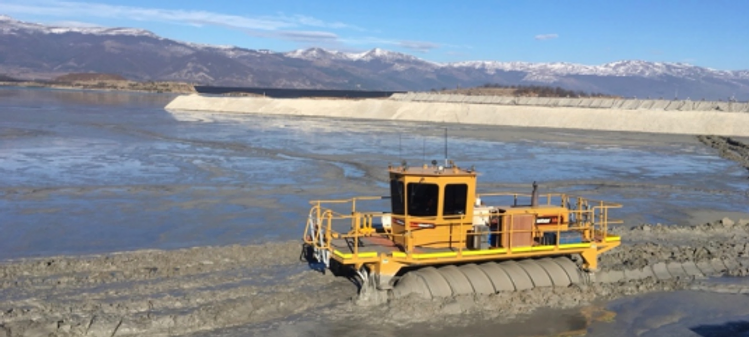
Hydraulic Mining9
Hydraulic mining uses water cannons used (often remotely) to direct high-pressure water to dislodge and move sediment or ore. The water carries the sediment through sluices or channels where the heavier minerals like gold are separated from lighter material. Hydraulic mining is particularly effective in areas where the deposits are found in alluvial soils, such as riverbeds and floodplains. It is used primarily in mining gold and tin.
In-situ leaching10
In-situ leaching involves injecting a leaching solution (typically a mixture of water and chemicals) into the orebody through wells. The solution dissolves the minerals, and the resulting mineral-rich solution (pregnant leach solution) is then pumped back to the surface for processing and extraction of the desired minerals. In-situ leaching is favored for its low capital cost and minimal environmental impact compared to traditional mining methods. However, it is applicable only in certain geological settings where the orebody is permeable and can be effectively leached without contaminating groundwater. It is widely used for uranium, copper, and water-soluble salts such as potash and halite.
Borehole extraction11
Borehole extraction is a technique of extracting minerals through deep, narrow wells or boreholes. It is often used in situations where traditional mining methods are impractical or too invasive. Compared to open-pit or underground mining, it has less environmental impact and can be used to access resources that might be unreachable with conventional mining methods. However, it also requires precise targeting and control to avoid unintended environmental impacts, particularly groundwater contamination. It is most commonly used to mine lithium, boron, bromine brines, crude oil, and gas.
Mining methods primarily associated with coal
While coal is not a focus commodity for RCF, the following mining methods are traditionally used to extract coal:
In strip mining12, layers of soil and rock are removed in long strips to expose and extract underlying minerals. Overburden above a coal seam or ore horizon is often drilled and blasted then removed by a dragline, shovel, or dozer push, followed by extraction of the exposed coal or ore by an excavator or loader. Mining proceeds in strips or follows a contour and is followed by backfill and reclamation.
Another extraction method uses a surface miner13: a large, specialized machine that integrates cutting, crushing, and loading functions. These machines extract minerals by removing the overburden and directly cutting the deposit. Surface miners are known for their precision and efficiency, and are effective in situations where drilling and blasting would be less efficient or environmentally viable.
Highwall mining14 is a technique that combines elements of both surface and underground mining. It involves the extraction of coal from exposed seams in the high walls of open-pit mines using a specialized remote-controlled mining machine that extends a cutter head into the coal seam and extracts the coal, which is then transported to the surface. This method allows for the recovery of coal left behind in open-pit operations, extending the life and productivity of the mine.
Underground Mining
In underground mining, tunnels or shafts are excavated deep beneath the earth’s surface to extract minerals from orebodies. The choice of a particular method of underground mining is based on:
- How well the method can extract ore while minimizing the inclusion of waste materials and the loss of valuable ore (known as selectivity)
- Support requirements to maintain the stability of underground excavations
- Dip (angle) and geometry of the orebody; and
- The order of operations and the progression of mining activities (sequence)
A key component of underground mining is the stope, an excavated space created by the removal of ore where the actual ore extraction occurs. The shape and size of a stope depend on the mining method used and the characteristics of the orebody, such as its thickness, depth, angle, and geological setting. The design and management of stopes are crucial for the efficiency and safety of the mining operation.
Advantages of Underground Mining
- Less environmental impact: Underground mining has a reduced environmental footprint compared to surface mining. It causes less landscape disruption and no visual scars like large open pits.
- Access to deep deposits: Underground mining allows access to mineral and ore deposits that are too deep to be mined by surface methods.
- Reduced surface land use: Underground mining does not require large areas of land to be cleared, preserving the surface for other uses.
- Less noise and air pollution at the surface: Since operations are underground, there is less noise and air pollution and reduced impact on nearby communities.
- More selective: Underground mining can be more selective targeting specific ore body while striving to minimize waste production.
Disadvantages of Underground Mining
- Higher costs: Underground mining is generally more expensive than surface mining due to complex logistics, the need for specialized equipment, and higher safety requirements.
- Safety risks: Safety risks include the potential for cave-ins, flooding, and hazardous air conditions.
- Limited working space: The confined space of underground mines limits the size of equipment that can be used and can complicate the extraction process.
- Complex ventilation needs: Ensuring proper ventilation to provide fresh air and remove harmful gases is a significant challenge in underground mining.
- Higher energy consumption: Due to ventilation, lighting, and pumping requirements, underground mining can be more energy-intensive than surface mining.
Underground Mining Methods
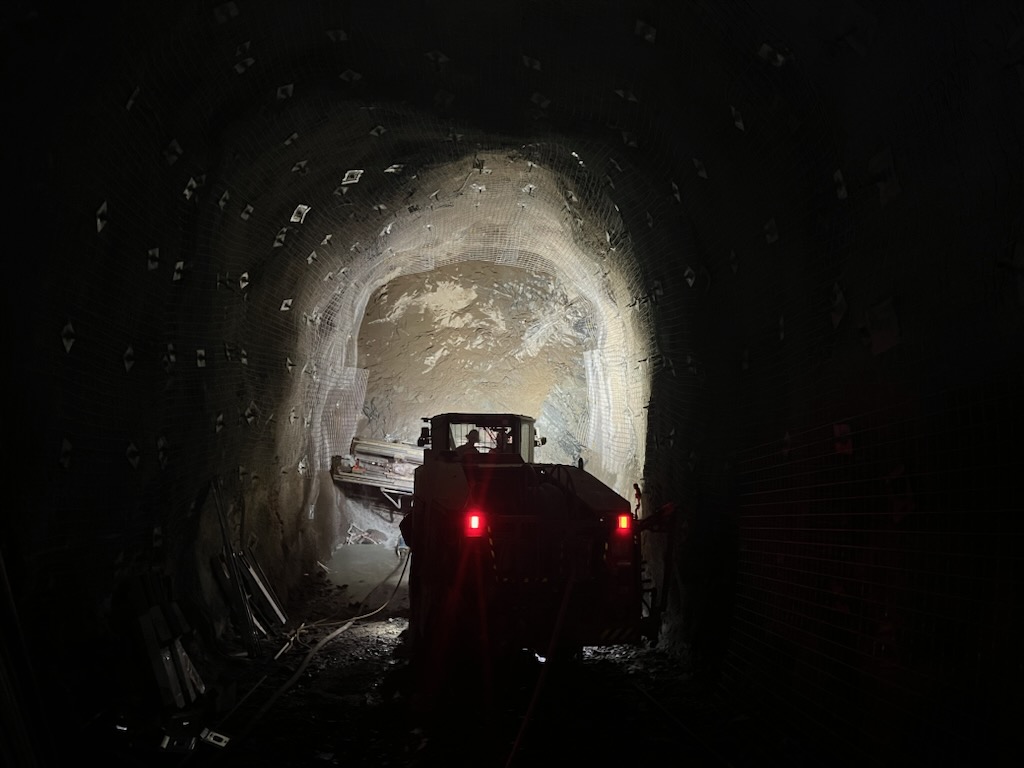
Sublevel Open Stoping (SLOS)15
Used frequently in steeply dipping orebodies, sublevel open stoping (SLOS) involves creating sublevels in the orebody, in which miners drill and blast the ore in a series of parallel horizontal slices from the bottom upwards, without filling the voids. This method is effective for mining a wide range of minerals, including gold, copper, and zinc, and is favored for its efficiency in ore extraction and flexibility in complex geological settings.
Sub-level Stope
Used for large ore bodies with a steep dip, regular shape, and well-defined ore boundaries. The ore body is divided into a series of horizontal sub-levels spaced at regular intervals where large stopes are blasted and backfilled to increase ore body recovery. The method typically involves dividing the ore body into primary and secondary stopes, which are mined in an alternating sequence, primary stopes are mined first, with secondary stopes acting as temporary pillars. After the backfilling of the voids left by the primary, the secondary stopes are mined, ensuring support for their extraction.
Long Hole Stope
Similar to SLOS, The Long Hole Stope method mines one level at a time. This is typically due to the inability of the orebody to maintain large openings without collapsing, or because the orebody does not present the required continuity which could compromise drilling.
Cut and Fill Stoping16
Cut and fill stoping is used in irregular or steeply dipping orebodies, and where the surrounding rock is not stable enough to stand on its own. Ore is excavated in horizontal slices following drilling and blasting. Waste rock or tailings are loaded into the stope while providing ground support for the excavation and a working platform for the next slice. This method is often used for high-grade deposits in high-value commodities including nickel, gold, and silver.
Block Caving17
The block caving method creates an extraction level beneath the orebody which allows it to collapse under its own weight into a series of chutes and underground rooms from which it is extracted. This method is cost-effective for large-scale, low-grade mineral deposits. It is particularly effective when the orebody is large and continuous, and where the orebody is weak enough to collapse easily. It is typically used in low-grade copper-gold porphyry deposits, as well as kimberlite diamond deposits.
Sublevel Caving19
Sublevel caving is a large-scale underground mining technique used primarily for extensive, low-grade orebodies that have a steep dip, regular shape, and large vertical extension. Mining starts at the top of the orebody and progresses downwards in a series of repeated steps. As ore is extracted, the surrounding rock collapses into the void, allowing for continuous ore recovery. Sub-level caving is especially effective for low-grade copper-gold porphyry deposits, nickel, and iron ore, where the orebody is consistent and large enough to justify the extensive infrastructure required.
Room & Pillar19
In room & pillar mining, “rooms” are excavated into the mineral deposit and separated by “pillars” of unmined material left to support the roof of the mine. Room & pillar mining allows for a high recovery rate of the resource while maintaining the stability of the mine structure, making it suitable for deposits where maintaining the integrity of the overlying surface is important. This method is used most often for relatively flat-lying orebodies with moderate to high stability, such as coal, salt, potash, and limestone.
Shrinkage Stoping20
Shrinkage stoping is used for steeply dipping orebodies with strong ore and rock structures. It involves mining upwards in horizontal slices, leaving broken ore in place to serve as a working platform and support for miners working above. This method is particularly effective for extracting narrow, high-grade veins of minerals such as gold, silver, and copper, where the ore needs to be extracted selectively and safely.
AVOCA Stoping21
AVOCA stoping is typically used in narrow orebody scenarios where traditional mining methods are not viable due to low mining production rates and/or poor orebody recovery. In this mining method, backfilling and drilling are conducted alternately, allowing for sequential extraction and filling, which maintains stability with improved ore recovery and production rates. Dilution is a key aspect to be controlled during AVOCA mining method applications Identifying the ore/waste boundaries after the blasting operation can be challenging in some cases. AVOCA is very effective for mining steeply dipping, narrow vein minerals like gold, silver, or base metals, where maintaining the integrity of surrounding rock and optimizing orebody recovery is crucial.
Technological Advancements
Mining as a whole is becoming more challenging because high-grade, easily accessible deposits have largely been mined. In fact, the average copper ore grade in Chile has declined 30% over the past fifteen years22. Now the focus is on innovations that allow for more efficient extraction and processing, making it economically viable to mine lower-grade deposits that were previously unprofitable. Technological advancements that make this feasible include:
- Automated and remote-controlled machinery
- Drones that can provide aerial surveys, mapping, and inspections
- Advanced drilling and blasting techniques with improved precision, better resource extraction, and reduced waste
- Real-time data analysis
- Environmentally-friendly processing methods
Taken together, these advancements also enhance worker safety by minimizing the need for human presence in hazardous environments, driving operational efficiency, reducing costs, and contributing to more sustainable mining practices.
Declining quality of mineral resources and the increase in demand for critical minerals driven by the energy transition are pushing the mining industry to transform itself. Innovation has become so critical that it has developed into its own industry sector: the Mining Equipment Technology and Services (METS) which is projected to generate revenues of $200 billion by 203023. The RCF Innovation strategy mandate is dedicated to investing in this sector, with the goal of finding companies leveraging innovation to make mining safer, cleaner, and more efficient.
Potential Impact of AI on Mining Methods
Artificial Intelligence (AI) is poised to have a significant impact on the mining industry, including the choice of mining method for specific projects. AI’s ability to analyze vast datasets and recognize complex patterns can guide the selection process by providing more informed insights into the feasibility and potential yield of various mining methods. For instance, AI algorithms can evaluate geological data and suggest whether methods like block caving or sublevel caving are suitable for a particular orebody24. This helps optimize resource extraction, improve safety, and reduce environmental impacts.
Pitcrew AI is an example of an RCF Innovation II investment that is leveraging AI: No matter the mining method, haulage and transportation are significant operational costs for mining companies, which use massive vehicles to move excavated materials. Tires alone are a major cost center – they can weigh over 4 tons and cost tens of thousands of dollars each. Pitcrew AI’s real-time IIoT monitoring and predictive maintenance technology allows mines to extend tire life and helps prevent the expense, operational, and safety issues that can result from a catastrophic tire failure.
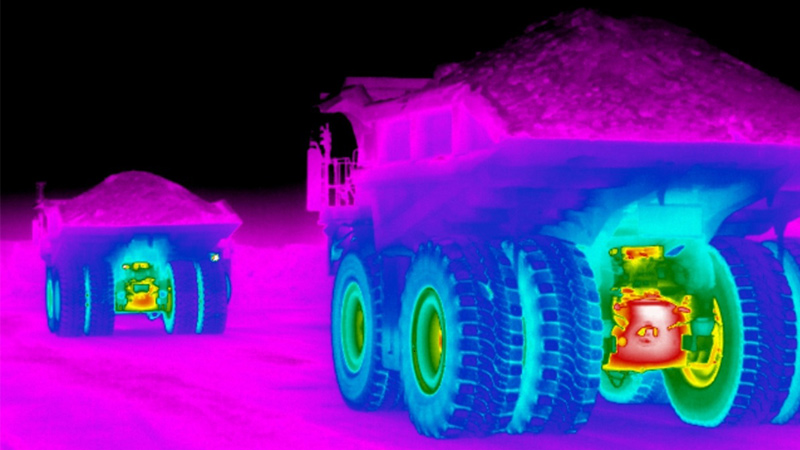
Mining Methods and ESG Considerations
The choice of mining method goes beyond economic and technical feasibility to include ESG considerations, such as safety, long-term environmental stewardship, and sustainability. The choice of mining method must balance water management, biodiversity, land stewardship, and worker health and safety with productivity and other ESG considerations. But it’s also important to understand that there typically isn’t a single best solution for issues relating to ESG, because there are always tradeoffs to consider. For example, while underground mining has a smaller land footprint than surface mining, surface mining generally provides a safer25 work environment.
Extracting Value
There are significant investment opportunities in the mining sector, with forecasts pointing to increased demand for critical minerals and metals driven by the energy transition, global middle-income growth and other macro-economic factors. However, successful investors will recognize that the metals and minerals sector is highly technical in nature, an understanding reinforced by the myriad considerations that go into the choice of a particular surface or underground mining method. General suitability issues, geotechnical factors, extraction rate, equipment selection, ESG, and other factors must all be considered when assessing a proposed method, and expert assessment by a multi-disciplinary technical team is critical to help assess, de-risk and optimize investment opportunities across all phases of mining.
Like what you’re reading? Subscribe to our top stories.
Source of Data
1 Britannica, Surface mining. https://www.britannica.com/technology/mining/Blasthole-stoping
2 LibreTexts Biology, 10.1: Mineral Resources and Extraction. https://bio.libretexts.org/Sandboxes/tholmberg_at_nwcc.edu/Introduction_to_Environmental_Science/11%3A_Conventional_and_Sustainable_Energy/10.1%3A_Mineral_Resources_and_Extraction
3 LibreTexts Biology, 10.1: Mineral Resources and Extraction. https://bio.libretexts.org/Sandboxes/tholmberg_at_nwcc.edu/Introduction_to_Environmental_Science/11%3A_Conventional_and_Sustainable_Energy/10.1%3A_Mineral_Resources_and_Extraction
4 Wikipedia, Surface mining. https://en.wikipedia.org/wiki/Surface_mining
5 Wikipedia, Surface mining. https://en.wikipedia.org/wiki/Surface_mining
6 Wikipedia, Surface mining. https://en.wikipedia.org/wiki/Surface_mining
7 Britannica, Surface mining. https://www.britannica.com/technology/mining/Blasthole-stoping
8 Britannica, Dredging. https://www.britannica.com/technology/mining/Dredging#ref622497
9 Britannica, Hydraulic mining. https://www.britannica.com/technology/hydraulic-mining
10 Wikipedia, In situ leach. https://en.wikipedia.org/wiki/In_situ_leach
11 Wikipedia, Borehole mining. https://en.wikipedia.org/wiki/Borehole_mining
12 Britannica, Strip mining. https://www.britannica.com/technology/strip-mining
12 NC State University, The demand for gold is growing, do we have a solution? https://delftia.wordpress.ncsu.edu/the-demand-for-gold-is-growing-do-we-have-a-solution/
13 Wirtgen Group, Surface Miners and Cross Application Miners. https://www.wirtgen-group.com/ocs/en-us/wirtgen/surface-miners-and-cross-application-miners-74-c/
14 International Journal of Mining Science and Technology, Highwall mining of thick, steeply dipping coal–a case study in geotechnical design and recovery optimization. https://www.sciencedirect.com/science/article/pii/S2095268617309047
15 Mineral Resources Education Program of BC, Underground Mining Methods. https://mineralsed.ca/site/assets/files/3448/undergroundminingmethods_me.pdf
16 Mineral Resources Education Program of BC, Underground Mining Methods. https://mineralsed.ca/site/assets/files/3448/undergroundminingmethods_me.pdf
17 Britannica, Block Caving. https://www.britannica.com/technology/block-caving
18 Mineral Resources Education Program of BC, Underground Mining Methods. https://mineralsed.ca/site/assets/files/3448/undergroundminingmethods_me.pdf
19 Mineral Resources Education Program of BC, Underground Mining Methods. https://mineralsed.ca/site/assets/files/3448/undergroundminingmethods_me.pdf
20 Britannica, Shrinkage stoping. https://www.britannica.com/technology/shrinkage-stoping
21 SidmartinBio, What is Avoca mining method? https://biosidmartin.com/what-is-avoca-mining-method/
22 IEA, Reliable supply of minerals. https://www.iea.org/reports/the-role-of-critical-minerals-in-clean-energy-transitions/reliable-supply-of-minerals
23 Grand View Research, 2023
24 Hindawi, Review on the Development of Mining Method Selection to Identify New Techniques Using a Cascade-Forward Backpropagation Neural Network. https://www.hindawi.com/journals/ace/2022/6952492/
25 Essential, Comparing Open-Cut Mining and Underground Mining. https://essential.construction/news/comparing-open-cut-mining-and-underground-mining/
Important Information
This information should not be deemed to be a recommendation of any specific commodity, company, or security.
This material is provided for educational purposes only and should not be construed as research. The information presented is not a complete analysis of the gold and/or commodities landscape. The opinions expressed may change as subsequent conditions vary. The information and opinions contained in this material are derived from proprietary and non-proprietary sources deemed by Resource Capital Funds and/or its affiliates (together, “RCF”) to be reliable. No representation is made that this information is accurate or complete. There is no guarantee that any forecasts made will come to pass. Reliance upon information in this material is at the sole discretion of the reader.
None of the information constitutes a recommendation by RCF, or an offer to sell, or a solicitation of any offer to buy or sell any securities, product or service. The information is not intended to provide investment advice. RCF does not guarantee the suitability or potential value of any particular investment. The information contained herein may not be relied upon by you in evaluating the merits of investing in any investment. There can be no guarantee historical trends will continue.
RCF Innovation II comprises RCF Jolimont Mining Innovation Fund II L.P. and RCF Jolimont Mining Innovation Fund II-A L.P. RCF Innovation I is not a legally established partnership and represents an extracted portfolio of investments of Resource Capital Fund VI L.P. (“RCF VI”) that was managed by the principals of Jolimont Global Mining Systems Pty Ltd before it was acquired by RCFM in September 2019. Two of the three principals currently manage RCF Innovation II in a substantially similar manner to RCF Innovation I. Total portfolio performance results for RCF VI are available upon request.
Investing involves risk, including possible loss of principal.
Contents