Earlier this year, Resource Capital Funds (RCF) has hosted a unique and exciting tour of mining sites for existing and potential investors. It is an opportunity for limited partners to get an up-close look at mines in action and better understand the scale, complexity, and technological advancements in modern mining operations.
This June, we led a delegation of investors on a tour through eastern Canada. This began with a day of informational meetings in Toronto and continued to site visits of gold mines in Ontario and Quebec, which allowed us to experience two very different types of mining operations. Also joining us on the tour were two of RCF’s partners, Jacqui Murray and Russ Cranswick. Jacqui is Head of Fund of the most recent vintage of RCF’s Private Equity strategy, while Russ manages the RCF Opportunities strategy. Prior to working in private equity, both spent substantial time in the field, Russ as a Mineral Exploration Geologist and Jacqui as a Geotechnical Engineer. They were able to provide more background on the geology and technology of the mines we visited, and their observations contributed to a richer experience for all of us.
Day One: Toronto
We spent our first day learning about the mining industry at the RCF offices in Toronto. In preparation for our visit to the gold mine in Quebec, we began with a presentation by RailVeyor, one of our portfolio companies in RCF Innovation II. RailVeyor manufactures a fully autonomous, electrically powered light-rail haulage solution for surface and underground applications in the mining industry. Their team gave us a great presentation on how their system works and can provide a cost-effective solution to key transportation requirements within mining projects.
Two members of the RCF Technical team, an in-house, multi-disciplinary group of mining specialists, hosted us for the next part of the presentation. Rafael Gradim, director and mining geologist, and Steve Axcell, a project development consultant, provided an overview of our decision-making process and how technical due diligence is applied to pre and post investment.
A mining trip in Toronto would not be completed without a visit to the Toronto Stock Exchange (TSX). Mining plays an important role within the Canadian city. We ended the day with a visit to Paradigm Capital, a research firm that RCF has worked with for years. The senior gold analyst who hosted us at Paradigm gave us a preview of the two mines we’d be seeing over the next two days: Côté Gold, an open-pit mine in Ontario owned by IAMGOLD, one of RCF VII’s investments; an underground gold mine in northern Quebec where the RailVeyor system plays an important role.
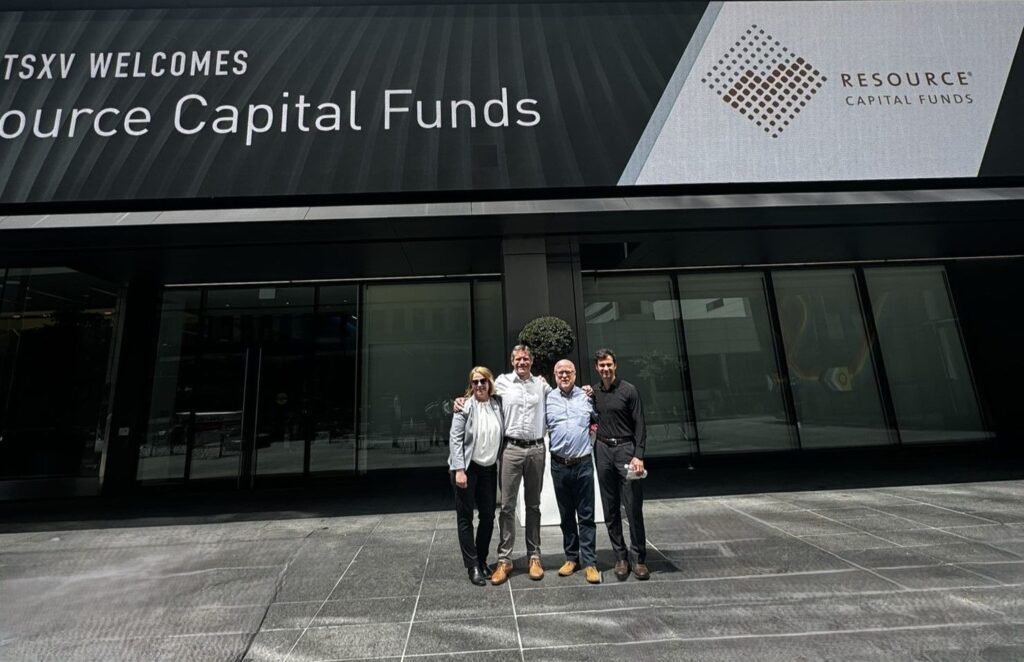
That evening, we boarded a plane for the town of Timmins, Ontario. Because the tour sites were all some distance from commercial airline hubs, we chartered a prop plane and left from Billy Bishop, a small regional airport in the Toronto Islands.
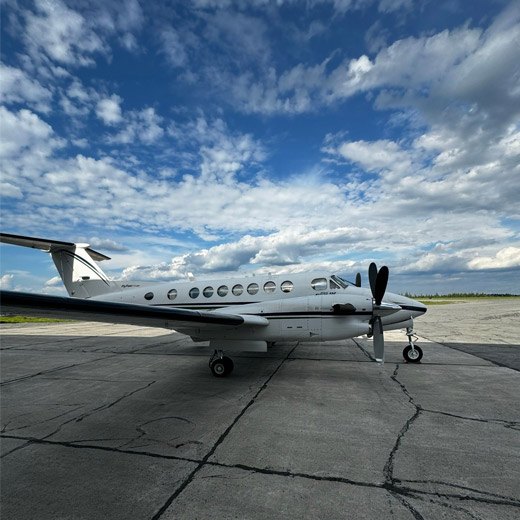
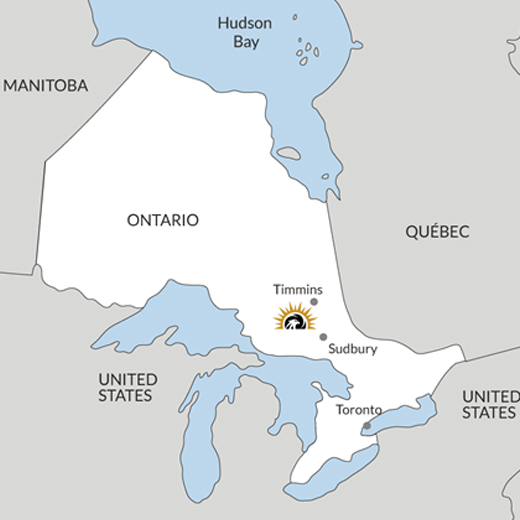
Day Two: Côté Gold Mine, Ontario
It was a two-hour bus ride from Timmins to Gogama, the municipality where the Côté Gold Mine is located. We arrived at the mine at 10 am and were warmly welcomed by the management team, who provided a comprehensive tour of this amazing mine.
Côté is an open-pit mine still in ramp-up phase, with the first gold pour completed on March 31. Even in its relatively young state, the scale of the mine was incredible. The pit dwarfed the enormous dump trucks, which are responsible for picking up ore and transporting it to be processed. Of the two dozen of these trucks on site, none are manned; they are operated autonomously according to a bespoke algorithm, and run 23.5 hours a day, with the last half hour reserved for fueling and maintenance. They’re designed to automatically account for any sort of variable they might encounter, from changes in the weather to a person on the track. All the trucks communicate back to the central control room, and that information is shared amongst the entire fleet.
The mine also uses autonomous drilling for excavation. Unmanned drilling rigs, operating according to a program, drill holes about 13 meters into the ground and drop a small explosive device into each one. These are set to detonate sequentially once or twice a week. Unfortunately, the day we were there was not a detonation day, but we were all deeply impressed with the efficiency and scale of the technology being used.
After visiting the pit, we went back to the processing facility to learn how ore is processed. Ore is simply rock that contains some amount of metal. In the case of this mine, gold isn’t found in nuggets, like in the movies, but in flakes. Once ore is excavated from the ground, it is taken through a series of grinding stages to break down large rocks into a kind of sand known as fine ore. Next, a centrifuge is used to help separate the gold from the rest of the ore. This gets 20-30% of the available gold. The rest is extracted using chemical processing to dissolve and separate the gold, which is then recovered using another chemical process.
The ore grade at Côté is 0.97 grams per tonne, meaning that for every tonne of ore that is dug up and processed, the result is slightly less than a gram of gold. After thousands of tonnes of ore have been processed – thanks to the work of some 600 staff members – the average amount of gold produced each day is the equivalent of a single gold bar.
All of us on the tour were amazed by the sheer scale involved in moving and processing the ore. To give you a sense of the size of the grinding mills, we had to walk up 10 flights of stairs to get to the top of one of them. We had to make a very deliberate effort not to look down through the grated staircases, which showed us exactly how high we were!
We were equally impressed with the safety measures in place. The management at Côté makes safety an absolute priority: Every employee on the site is outfitted with a safety device. If they feel they are in danger at any time, they can press a button and every autonomous vehicle within a 500-foot radius will shut down automatically.
There are about 600 people who work on the Côté Gold site in two different shifts. Around 20-30% live on site; others live locally. The mine is located on Treaty 9 territory, the traditional lands of Mattagami First Nation and Flying Post First Nation. As part of their permitting and social license, Côté Gold pledged a percentage of jobs to First Nations people. The mine has very close ties to the local community, with executives and staff alike participating in festivals and other local events.
After a fascinating day at Côté, we climbed back on board our bus and returned to Timmons. From there, we re-boarded our plane and headed for Quebec. There, we soaked up some of the French-Canadian culture by way of dinner at a nice French restaurant before heading back to our hotel to get ready for our next mine.
Day 3: Underground Gold Mine, Quebec
We arrived at a scenic lakeside town where mining is the main source of income. Gold has been mined there since the 1920s, and more recently, copper, lead, and zinc have become increasingly important.
The gold mine, which has been operating since 2013, is just a ten-minute drive from downtown—very helpful as our tour started bright and early at 7:30! RCF does not own this mine, but we have a close relationship with the company that does. As an underground mine, it made an interesting contrast with Côté. Like the operation we saw the day before, this mine is also known for its efficiency, which is due in part to use of RailVeyor’s autonomous light-rail material hauling system, the largest in use at any mine.
We got our first taste of the mine’s capabilities when we stepped into its astoundingly fast auxiliary elevator, which operates at 750 meters per minute (the main elevators operate at an incredible 2700 meters per minute!). We were at the bottom of the 800-meter mine shaft almost before I realized we were moving.
The underground mine is divided into levels, with each level representing 10 meters of elevation drop. To date, the lowest level of the mine is 143 — an incredible 1.43 km below ground. Fast as they were, the elevators only go to level 8 and today’s destination was 120. So, after stepping off the elevator, we climbed aboard a truck that would take us to 1200 meters below the surface.
Our limited partners were thunderstruck at how much activity we saw. There were multiple types of vehicles, including trucks, loaders, and bulldozers, even though the mining tunnels we drove through were barely wide enough for a single truck. As a result, there are a lot of warning lights and constant honking as trucks go around turns to ensure that anyone coming from the other direction knows they’re there. The tunnels are pocketed with alcoves, so that if two trucks find themselves facing each other, one can back up and move out of the way.
It was extremely dark, and damper than I would have expected. In part, this is because the mine sprays water around to keep the dust down. It’s warm, in some areas almost stiflingly so, especially since we were wearing heavy protective equipment. Air is recirculated, which causes strong drafts in certain places, and the atmosphere is tinted with the faint smell of ammonia, a byproduct of the explosives used. All told, it was an otherworldly experience, like nothing I’ve encountered on the surface of the earth.
For transportation purposes, the ore needs to be broken down into relatively small bits at an earlier stage than at the Côté mine. To see that process in action, we went to the rock hammer room on level 120, which is about what it sounds like: an enormous room filled with huge chunks of rock, two huge tungsten-tipped robotic hammers, and another robotic arm for grabbing and cutting. These are controlled by two employees using, of all things, Xbox controllers. Ore is delivered from above by a chute and from below by trucks, then the rock is cut and pulverized until it’s small enough to fall through the 18”x18” grates that make up the floor.
This is the point at which the RailVeyor trains come in. Since the mine is underground, many of its levels lack the space needed for trucks and other large vehicles. RailVeyor reduces dependency on trucks and contributes to higher operating profits by reducing fuel and maintenance expenses. It has also contributed to a safer mine as it is operated remotely and reduces the amount of dust and emissions in the air.
Most impressively, the Railveyor system has achieved a 39% reduction in mine-wide emissions compared with diesel trucks – a significant step towards reduced greenhouse gases. Additionally, these results are achieved with an almost 75% reduction in opex compared with traditional truck haulage.
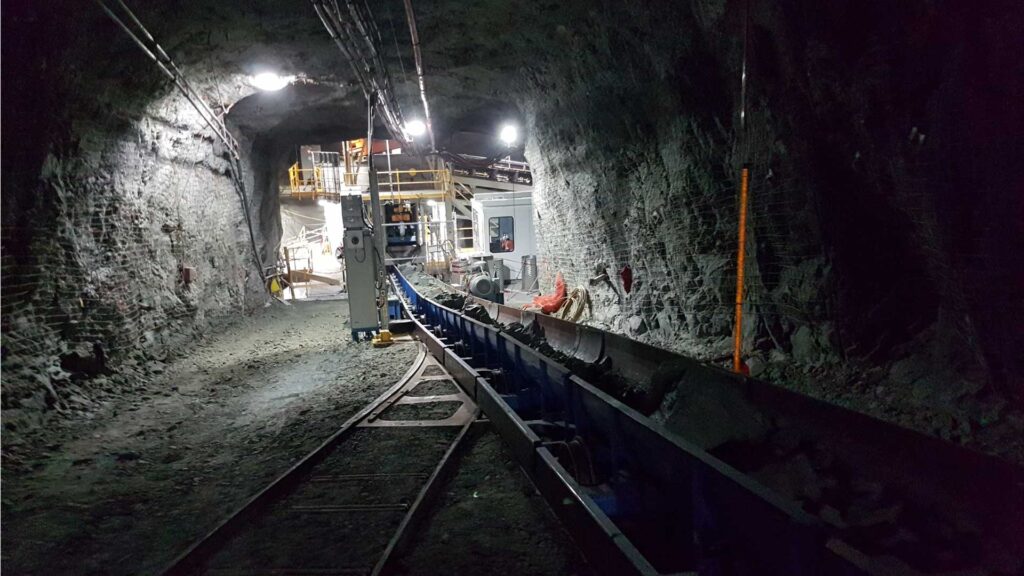
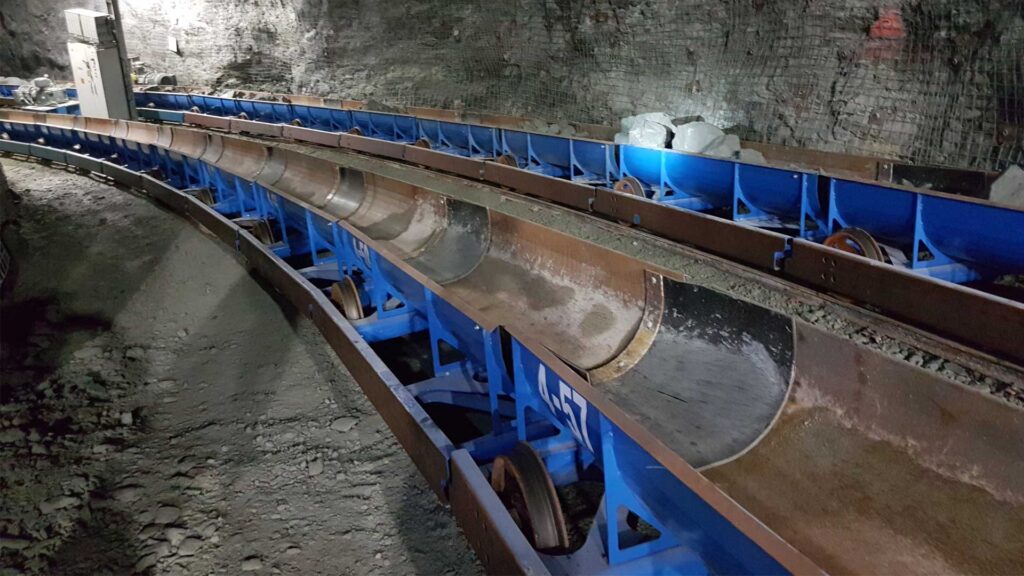
Once the ore has been reduced in size, RailVeyor transports it to the mineshaft. Each train is 166 meters long, almost the length of two football fields, and is used to transport ore from level 120 up to level 72, about 50 stories, where the mine shaft is. The rail system covers about three kilometers altogether and uses a set of tunnels exclusively created for RailVeyor – almost like its own subway system. From the bottom of the mineshaft, the ore is brought up by a hoist connected to the elevator. Once on the surface, it is transported to the onsite mill for processing. The mill began processing ore just last November and achieved commercial production in the first quarter of 2024.
The average grade at the mine is around two grams per ton. Thanks, in part, to its RailVeyor system, this mine is one of the lowest-cost producers among its peers. As with Côté, and all mines, it is efficiencies like these that allow it to be profitable.
Closing Thoughts
On my way home, I reflected on the irony that gold, one of the earliest mined metals, is now being extracted using some of the most innovative techniques available. Our modern world couldn’t exist without mining and the metals it produces, but most tend to take it for granted and very few people are aware of the cutting-edge technology and massive scale of processing required to make it economical. Experiencing the enormity and complexity of these mines really brought home how much work goes into supporting the world we live in.
These visits also reinforced how important it is for these mines to operate efficiently. Worldwide and across all metals, much of the low-hanging fruit has already been discovered and mined. These days, we need to look to lower-grade ore like that which is being mined in Ontario and Quebec. Efficiency is the key to making these projects economical, hence the intense focus of these mines on automation and innovation. RCF contributes to this efficiency, both by providing needed capital but also, just as importantly, by how well we understand the industry. We leverage that experience to help our portfolio companies operate more effectively, supporting them with the knowledge, strategies, and connections they need to thrive.
Important Information
This information should not be deemed to be a recommendation of any specific commodity, company, or security. This material is provided for educational purposes only and should not be construed as research. The information presented is not a complete analysis of the energy transition and/or commodities landscape. The opinions expressed may change as subsequent conditions vary. The information and opinions contained in this material are derived from proprietary and non-proprietary sources deemed by Resource Capital Funds and/or its affiliates (together, “RCF”) to be reliable. No representation is made that this information is accurate or complete. There is no guarantee that any forecasts made will come to pass. Reliance upon information in this material is at the sole discretion of the reader.
None of the information constitutes a recommendation by RCF, or an offer to sell, or a solicitation of any offer to buy or sell any securities, product or service. The information is not intended to provide investment advice. RCF does not guarantee the suitability or potential value of any particular investment. The information contained herein may not be relied upon by you in evaluating the merits of investing in any investment.
Investing involves risk, including possible loss of principal.