Alessandro Dotta, Director, Mining Engineering at Resource Capital Funds (RCF), and a graduate of the Universidade de São Paulo, has worked in the mining industry for almost two decades. He has held key positions at several prominent mining companies, including Sandfire Resources, EMR Golden Grove, and Vale. He was Corporate Planning Manager at AngloGold Ashanti before joining RCF in 2023.
Here he talks about his role as a mining engineer, how he became interested in the field, and the value that mining engineers provide to a project over the mining lifecycle.
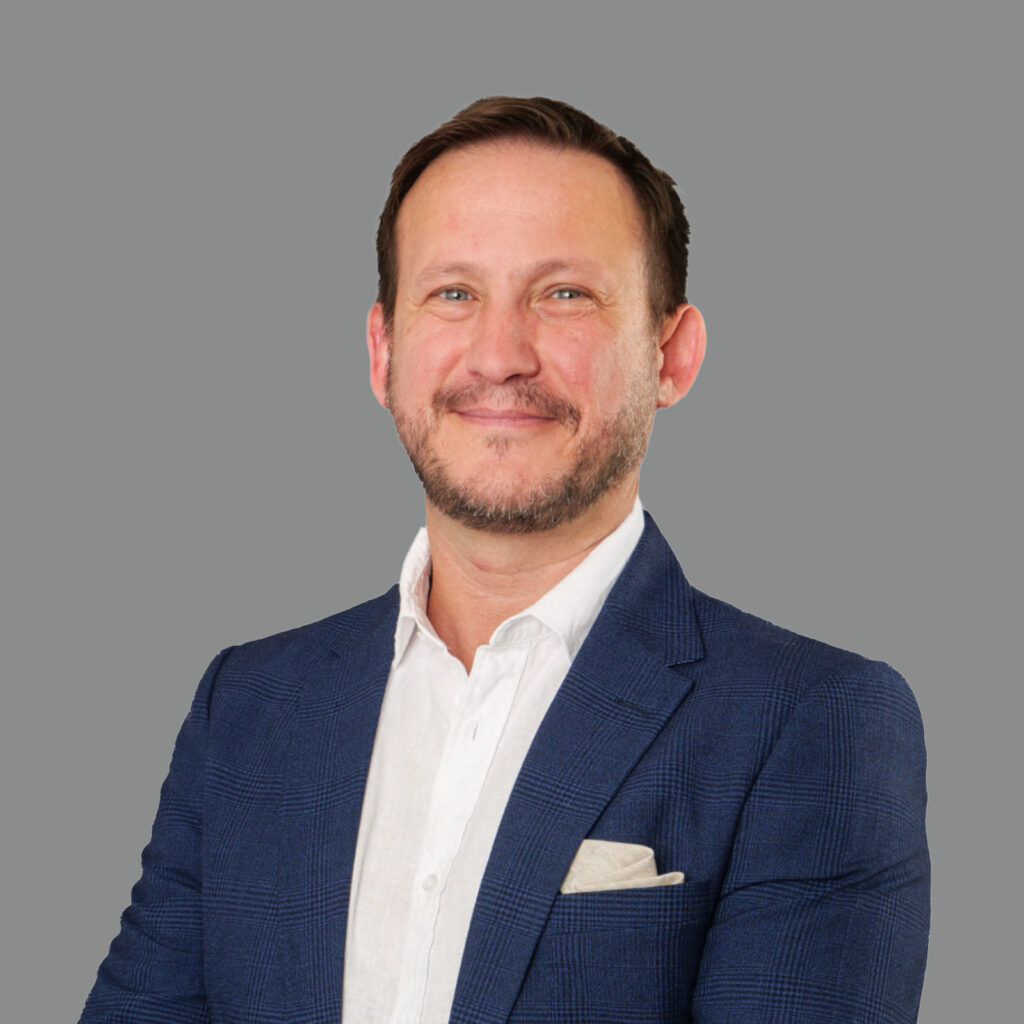
In your own words, how would you describe mining engineering?
A basic definition is that mine engineers plan and manage the extraction of mineral deposits. Mine engineers are people with the ability to create a long-term, profitable mining business that maximizes safety, optimizes costs, and delivers financial returns to investors.
We also make sure our projects align with rules and regulations and help make mining more environmentally responsible.
How did you get started in this field?
When I was a kid, I loved electronics and I loved computers. Originally, I wanted to be an electrical engineer, but my family has a little bit of history with mining. My grandfather migrated from Italy to Brazil, where he started a business producing batteries. The batteries used graphite to make the internal core electrode, so he opened a graphite mine. I never met my grandfather, but my father always talked about how much he loved geology and mining.
After I finished the technical studies for electronics, I started university. The first two years were in a basic accredited engineering program. After the first year, I needed to pick a field to specialize in. And I thought, why not a mining engineering program?
I ended up really enjoying it and I’ve been a mining engineer for almost 20 years now.
Can you describe what mining engineers do in the different phases of mining?
Mining engineers are involved in many stages of mining, although during the very early stages of exploration and drilling before there are any results, we’re on standby. Once we have the initial block models1, some drilling results, and some basic geotechnical information, that’s when mining engineers get involved.
If the results are positive, we follow with other studies: scoping, pre-feasibility, and feasibility stages. Each stage gets more accurate data than the previous stage. This is when we narrow the certainties and assess the basic economic, environmental, and social aspects of a potential mining operation.
At the end of the feasibility stage, it’s critically important to understand the potential challenges, and the big opportunities associated with a project.
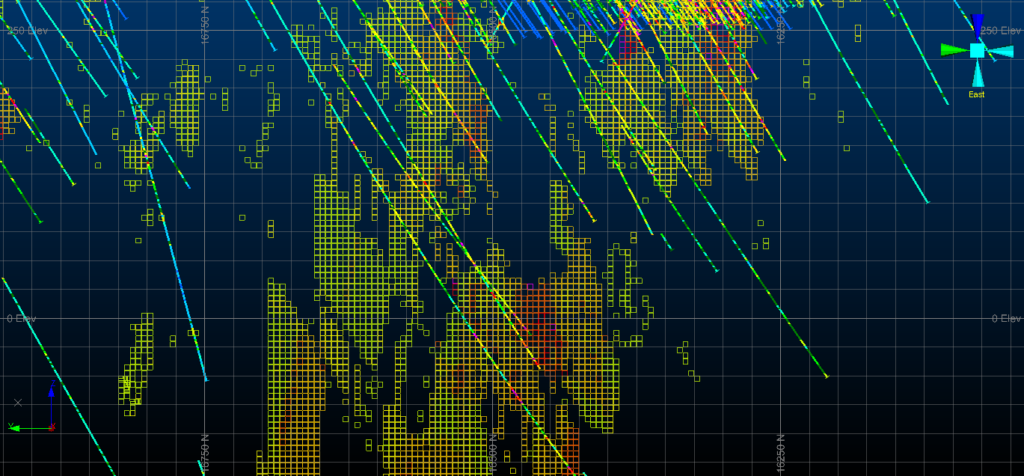
Once the studies are completed, we get to the implementation phase, where we’re constructing the mine, and this is where mining engineers become heavily involved. It’s when we move from what’s on paper to reality, and there is usually a lot of adjusting that needs to be done along the way. This is challenging, and you really need a team that is experienced with the implementation stage—building the mine and ramping up mining operations. Once you get these issues solved, you get to the point where production is stable.
At that point, a lot of mine sites will change their management teams. You go from a mine operations team that is focused on implementation and getting everything up and running to one that is focused on hitting production targets and functioning as an operating mine.
Tell us about a mine’s blueprint, and some of the key things you do to build up that blueprint.
It’s basically a schematic of how you’ll build the mine, and usually, those blueprints are based on certain technical assumptions around stope size, distance from your decline to the ore body, pillar sizes, what the angles are, and so forth.
The blueprints show how the mine is supposed to be built, but these assumptions can change. The geological and technical information is limited by the distance between your drill holes. Meaning, the farther away from these drill holes you get, the more uncertainty you have. As you start to open the mine, you face challenges that you might not have been able to predict. You may find faults you weren’t expecting, for example, and your engineering team has to work with your technical team to figure out the best solution for crossing this fault.
What are the key investment decisions or assessments investors are making at these stages? How do they rely on engineering assessments to make those decisions?
During the study phases, investors are relying on mine engineers and technical specialists to look for red flags in the assumptions that could lead to flawed conclusions—what are the cost models, what are the known and unknown factors, how are the financial models built, etc. The mining engineers are doing due diligence. We’re checking the fleets. We’re asking, are the trucks the right size? Are the mining methods appropriate for the ore body type? Are the dilution assumptions aligned with what we would expect from the selected mining method? How big can a stope be? Is the scheduling appropriate? And so on.
For example, we had one study that assumed dilution was 0% and assumed mine recovery was 100%. This was an immediate red flag because 0% dilution and 100% recovery are virtually impossible.
Once we get to the feasibility stage, we’re much less likely to have red flags because we’ve completed a very rigorous assessment. There may still be some variables depending on who performed the study and what assumptions they used, but usually at this point, we know we can make money and we’re narrowing our understanding of the project.
Mining engineers have a different perspective than, say, geologists. We like to say that mining engineers kill geologists’ dreams [laughs]. Then, the mining engineers try to get too fancy with a concept and geo-technologists kill the mining engineers’ dreams! The point is effective mine planning requires many layers of technical experts reviewing each other’s work during each phase. This helps everyone remain objective and avoid becoming too attached to a particular assessment.
What are the biggest mistakes mining engineers and/or investors can make when assessing opportunities during a particular phase?
I think the biggest mistakes occur during the project implementation phase. This typically happens because assumptions were not challenged during the study phases. Very often, you’ll find mistakes in those studies.
Let’s say somebody makes a wrong assumption about dilution . That will result in extra tonnage once you start mining. Let’s say they assume a 5% dilution. But actually, you have a 15% dilution. That means that you have 10% extra tonnage being mined with your ore, which is an extra 10% that needs to be transported to the processing plant. Now you may be in a situation where your fleet doesn’t have enough capability to meet your targets. You’re also delivering ore at a lower-than-expected grade to the plant. This could be a big issue for the processing plants as well because it could decrease recovery, increase costs, etc.
For that reason, I think implementation teams need to be very experienced. They need to really know the commodity they’re working with so they don’t just take what’s in the study at face value. This is where RCF can provide a ton of value.
Do different metals and minerals require different engineering solutions? Are some more complicated than others?
Yes, absolutely. Different commodities definitely call for different mining methods. Let’s take iron ore as an example. These are massive deposits, so you’ll usually see open pits.
Then you look at gold deposits. Depending on the orebody type, and if budget permits, an open pit method may work. Later in the project, however, if you have enough grade and material, an underground mine may make sense. Once you select underground mining, there is then an entire range of mining methods you could apply depending upon orebody characteristics.
How is technology changing mining engineering?
There have been some significant changes over the past few years. We’re seeing more electrification of mines and mining transport. Not that long ago, we communicated on two-way radios and had to do virtually everything manually. Now we have wireless systems inside of mines that give us amazing control.
In particular, technology is making mines much safer. We’re able to predict and prevent dangerous events in ways that were not possible until quite recently. In the past, for example, we would have had to send someone in to physically check the temperature and the ventilation. Now we can check those conditions remotely and keep tabs on exactly where people are working in the mine. If we know what the temperature is, we can limit the amount of time people work to avoid heat stress.
If you look at the software that is used in mine design and planning these days, it’s incredibly sophisticated. It can be used for pumping systems, for ventilation, to calculate variances—all kinds of things are becoming easier and increasing the amount of telemetry data we have access to. This makes it easier to manage variances through a feedback system, which helps increase the accuracy of financial models.
We’ve already got companies producing helmets with sensors that can read your heartbeat or measure gasses in the atmosphere. Artificial intelligence and machine learning are already making an impact on mine safety. Pretty soon, we will have self-driving trucks that will monitor and respond to external factors like vibration, temperature, atmosphere changes, real time telemetry, etc. Some companies are already doing predictive maintenance like Pitcrew AI, a portfolio company in RCF Innovation II, that uses AI to help avoid tire failure. The RCF Innovation team invests in companies like these that are aiming to make mining safer, cleaner, and more efficient – it’s an exciting time in our industry and we’re much more advanced than people outside of our sector may realize.
What is the hardest part of your job? What’s the most fun?
I think the hardest part of my job is that we review lots of private, off-market deals. We have a massive number of opportunities to assess given the RCF brand in the mining sector. And, our investment teams are quite selective. We’re always being asked for our opinions on a particular project, what mining method makes most sense, etc. It can be quite challenging to decide how to prioritize, but also makes it exciting.
I would say the rewarding part is that we have a lot of different types of projects. In the past, I worked for Sandfire, which only mines copper, and for Anglo Gold Ashanti, which only mines gold. At RCF, we’ve invested in over 30 different commodities across more than 50 countries and over 220 investments. That kind of variety is very rewarding. For a mining engineer, it’s like being a kid in a candy store!
What is your favorite mining method and why?
It’s a lot of fun designing blasts, and then, of course, doing the actual blasting [laughs]… so I would have to say sub-level open stope is the most fun. You get decent size stopes and decent speed. Long-hole open stope is also a really good one.
If you look at a method like narrow vein, it’s a little trickier. It’s easier to make mistakes during a blast and it’s difficult to keep up consistent production. There are days that everything goes smoothly then days when the stopes freeze, and you need to change to a new stope.
Finally, what is your favorite metal and why?
I’d have to say either gold or platinum. Did you know they do not come from this planet? They originated in a particular type of supernova and were part of the primordial formation of our planet. So that means that the gold or platinum you wear on your finger is older than the sun.
Pretty cool, right?
Source of Data
1. A block model is a three-dimensional model of a deposit or mine that is divided into regular blocks. These blocks represent the geological characteristics of the area and are used for resource estimation, mine planning, and production scheduling.
Important Information
This information should not be deemed to be a recommendation of any specific commodity, company, or security. This material is provided for educational purposes only and should not be construed as research. The information presented is not a complete analysis of the energy transition and/or commodities landscape. The opinions expressed may change as subsequent conditions vary. The information and opinions contained in this material are derived from proprietary and non-proprietary sources deemed by Resource Capital Funds and/or its affiliates (together, “RCF”) to be reliable. No representation is made that this information is accurate or complete. There is no guarantee that any forecasts made will come to pass. Reliance upon information in this material is at the sole discretion
of the reader.
None of the information constitutes a recommendation by RCF, or an offer to sell, or a solicitation of any offer to buy or sell any securities, product or service. The information is not intended to provide investment advice. RCF does not guarantee the suitability or potential value of any particular investment. The information contained herein may not be relied upon by you in evaluating the merits of investing in any investment.
Investing involves risk, including possible loss of principal.